How healthy is your SprayFoam?

How healthy is your SprayFoam?
Sprayfoam has been a huge player in the home insulation industry, and is projected to grow by 4-6% CAGR through the next decade (marketsandmarkets.com). It is used as insulation (R-3.8 for open cell and R-7 for closed cell), and can be an air barrier and/or vapor barrier when applied properly (Johns Manville).
Bud Offermann is President of Indoor Environmental Engineering, a building science consulting firm in San Francisco. He gave a very informative interview on healthyindoors.com in July of this year, on material from a paper he presented at the International Society of Indoor Air Quality and Climate’s (ISIAQ) Indoor Air 2022 in Kuopio, Finland in January. You can read and download the paper here. Because of his experience with high variability in the application of spray foams and ensuing problems with chemical emissions, he can’t recommend spray polyurethane foam (SPF) to insulate your home. This article is based on his presentations.
Some SPF installations result in chemical emissions that cause odor and irritation and that are expected to persist for decades. Therefore, it’s important to research and consider before contracting for spray foam insulation. Can you imagine ruining your well-loved or newbuild home with something as permanent as spray foam?
There are two components of spray foam, which we can term A-side and B-side. These are stored in two different containers and fed through two hoses to the spray gun, where they are mixed as spraying takes place. The A-side is isocyanates, which are very reactive; they evaporate quickly and don’t hang around after application. These chemicals are mainly a problem for the applicators, who need to wear fresh-air breathing apparatus to avoid breathing them. The B-side is a resin which has the fire retardant, reactants and additives. These are the components that remain in the installed foam and off-gas over a period of time.
The main chemicals causing problems are allylchlorides, the fire retardant TCPP, BDMAEE (an amine created by breakdown of TCPP), and 1-Chloro-2 Propanol. These can cause eye and nose irritation. The emissions can last at a slow rate for 50-100 years. Temperature causes an increase in irritation and odor (summertime is worst).
Causes of offgas problems are hypothesized to include:
- If the two components are mixed in the wrong concentration, it will not cure properly. For example in closed cell foam, too much A makes the foam fragile and brittle. Too-much B makes the foam too gooey.
- Storage of the resin (B) in the warehouse possibly allows water contamination (hydrolysis of the TCPP). Addition of water can create 1 Chloro-2 Propanol or allylchlorides. These substances can cause allergic reactions and continue to occur months or years later as the foam off-gasses.
- Closed cell foam should not be installed in thicknesses greater than 3”, otherwise the interior of the foam layer will not cure. Multiple passes are needed to achieve thicker application, but sufficient curing is needed between layers, otherwise uncured foam inside the layers will continue to off-gas.
- Sometimes the applicators switch between open and closed cell foam without changing the transfer pump or hoses. They only change the B-side (resin) drum and start spraying, which makes the product in the pump and hoses an unproven mixture of open and closed cell.
- Sometimes applicators buy the B-side and then add more chemicals for “winterizing” the foam. This is adding chemicals after-market, which will invalidate any warranty on that foam.
If you are experiencing bad air quality after spray foam application in your home, the first step is to test. Testing will let you know the level of the problem and if litigation is needed, proper air testing is required. Air samples are gathered with windows and doors closed, supplemental attic ventilation turned off, no air cleaners running, and normal house HVAC running. There are specific chemicals to test for, including VOCs excluding isocyanates and formaldehyde, also samples should be gathered in different rooms and outdoors as a baseline. After the air is sampled, an 8x8” chunk of foam is removed without disturbing the surface of the foam, to send to the testing facility (Berkeley Analytical is one recommended lab). You should also get the material safety data sheet (MSDS) for the foam, which should disclose all non-proprietary ingredients.
If emissions of SPF continue to cause problems, as an expert in home inspection and remediation, Mr. Offermann states there are two solutions:
- remove the insulation and the substrate, because the substrate absorbs some of these chemicals (very costly) OR
- attach a foil faced gypsum or rigid foam board against the trusses/studs to contain/reflect the gasses.
If you are sensitive to chemicals, spray foam is probably not the best choice for your home. However an alternative is to use foil-faced foam board. Because the foam board is made in the controlled environment of a factory, then tested, you can get the same insulative properties with much less chance of continual off-gassing . Foam board doesn’t have air barrier properties because of the way it’s installed, but air barriers can be achieved with other non-chemical methods.
In conclusion, further research on the chemical reactivity of TCPP and its suitability as a fire retardant is needed. Where is hydrolysis occuring? Proper storage of the B-side product and training of the application team is necessary because once spray foam is applied, emissions are unhealthy and removal can be very costly.
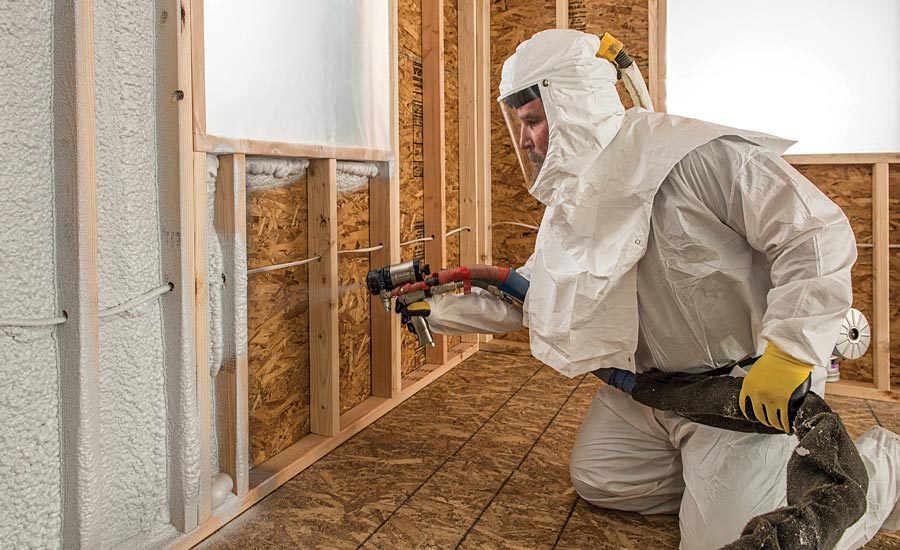
Photo from Johns Manville